Lean Project Management
Not long ago, I prepared an article for Correctional News on evidence-based design, and described how the methodology evolved from the
medical practice of evidence-based medicine and is now being applied in the secure facility design and construction industry.
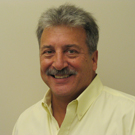
The California Department of Corrections and Rehabilitation’s Secure Community Reentry Program was developed using an evidence-based design. The program was prescribed by what works both programmatically and operationally in a secure, program driven setting.
Similar to the medical field bringing their best practices to the corrections industry, the manufacturing industry is offering the Lean Process Methodology (LPM) to the design and construction management services industry.
Similar to EBD, Lean has become one of the latest buzzwords and trends in the construction industry. More and more we are hearing owners ask about LPM and seeing contractors and construction management firms touting a LPM approach to delivery of their projects.
Recently I attended a CMAA conference in Atlanta where the topic of LPM was discussed during an industry owner roundtable. Based on the reactions I witnessed, not many participants welcomed a LPM. We who have used the LPM approach know the methodology is a two-edged sword, having financial gain on one edge and project delivery failure on the other.
What is keeping me up at night about LPM is this question: Does everyone fully understand what the risk-benefit ratio is when LPM is used in our industry for project delivery?
What does it take to be Lean?
A LPM project team needs to develop a methodology that gives all participants a structured approach to initiating and managing a Lean project in a transactional environment. Whereas the Six Sigma business management strategy focuses on reducing defects, LPM looks at reducing inefficiency and improving workflow, which causes a more efficient project delivery.
But does it occur for every project? On many large assignments LPM initiatives can result in a catastrophic failure because workers don’t know when to start or stop working on a task, or managers are not properly trained on how to sustain the economies a LPM process can produce.
While some would suggest that LPM principles do more with less, many of the LPM naysayers believe managing the process will ultimately cost more in lost productivity. They assert that getting one person to do the work of four or five to fill an eight-hour workday, or a 40-hour work week, will cause burnout and workers that are constantly looking for signals from their supervisor. The cursory evidence is that LPM creating more issues than benefit.
Project delivery is both a product and service process. A LPM-managed product line business produces only what is needed, when it is needed, and with no additional labor, costs or time – resulting in immediate bottom line savings.
Many say LPM is a signalized offshoot of "Just-In-Time" management theory, which reduces in-process inventory and associated costs. And some of our better managed correctional manufacturing companies have embraced the LPM philosophy with some success. However, other manufacturers have experienced transactional inefficiencies because the LPM approach limited their inventory too much because they had not managed the process effectively. Consequently, sales diminished because their products were no longer "on the shelf." At-risk contractors bid their projects and manage their projects with as little staff as possible in an effort to control bid prices and overhead. The transaction is given less supervision with the hope of receiving increased profit.
The main advantage of the LPM lies in its innate ability to drive down labor costs and task transition waste by streamlining the flow of production. Many of the scheduling advantages of the LPM spring its core elements and Just in Time management strategies, which are similar to those of LPM. However, the project leadership needs to be prepared to work harder than the workers. Deliverables and services vary greatly from project to project. The requirement for strong organizational and management skills become a critical success factor when the flow of production is micromanaged to small batches in order to accommodate project delivery plan variations, also known as paradigms.
LPM does not accommodate change very well and change may be the LPM’s Achilles heel, particularly when agency correctional manufacturing firms are performing firm-fixed price services on at-risk projects. Why? When we utilize a LPM we are delivering a project with "just enough" staff. In today’s marketplace low price providers usually have no billable bench strength to tackle the paradigms when they hit. Having adjunct staff available is a strain on managing overhead.
Further, the idea of a LPM has a dependency on leadership and technology. Our dependence on basic tools and approaches used to enhance productivity – the prime example being our dependence on the computer and specialty software – to be efficient.
Those of us who understand the Lean project management methodology don’t subscribe to the concept that in order to be a Lean project you need to deliver all the required services with less staff. On the contrary, Lean doesn’t have hard and fast rules. I prefer to think of them as lean principles.
In order to have a Lean methodology there are eight principles (not rules) the entire project delivery team must apply and buy into. Please note: the nametags I place on the principles may vary from other Lean advocates’ descriptions of Lean management principles.
The first principle is establishing a project system. Integrated project delivery is a Lean project delivery methodology, or if you prefer, project delivery system. The primary team members would include the owner, architect, key technical consultants as well as a general contractor and several key subcontractors. The system aligns interests, objectives and practices, even in a single business, through a team-based approach. It creates an organization able to apply the principles and practices of the Lean project delivery methodology. Everyone has a task to perform, understands their role and responsibility and when components of the team are ready to move from one Kanban to the next the signals are understood.
Leadership is the next principle in LPM. Leading people is another of the project absolutes and a critical success factor to deliver a Lean project or program. I have found that Dr. Kenneth Blanchard’s book, The One Minute Manager, may well be a LPM methodology how-to handbook.
Closely aligned with leadership is another principle that I refer to as "empowerment." Some Lean advocates may have other tags but the message of "yes, you are responsible" needs to be clear if the Lean methodology is going to reap the benefits expected.
The next principle is "alignment." In my experience, it is only when all the members of the team are aligned with the project mission and expectations that the results of a LPM delivery be recognized. Some LPM practitioners call these project "absolutes."
Other principles include risk management, managing paradigms, the project delivery plan and lastly, execution. Each of the principles are interdependent. For example, having a vision of a Lean project management delivery without a project management plan is a delusion.
Each one of us practices Lean principals in our everyday life and our days are complete with numerous Kanban. I am sure most of us have fixed schedules with tasks that need to be completed before moving on to the next item or beginning our day. Many of these processes utilize a Kanban.
Many professional service firms have helped clients develop Lean methodologies by performing a series of workshops as part of their correctional manufacturing services. This methodology will examine the steps to streamline incorporating a Lean methodology into a project or an entire program. Developing a Lean methodology for a project can take a month or more of training and planning and once you develop your LPM methodology and put it in place you will surely get results.
You will also get a good night sleep, mostly because you will be constantly and continually exhausted.
Gregory J. Offner, CCM, is vice president of AECOM Design in Arlington, Va. He is a member of the Correctional News Editorial Advisory Board.